Widely-used illustrations of what’s changed most in American home building in the 100 years between 1918 to 2018–a hard hat and a Skilsaw–draw a chuckle and a nod of resignation from many audiences as they have to admit how little has changed.
Ed Hudson, who heads up market research at Upper Marlboro, Md.-based Home Innovation Research Labs, and who has been in the cross-hairs of what’s changed and what hasn’t in home building for more than 20 years has this to say about it [the bold-facing below is mine].
We still build with lumber above-grade and concrete at- and below-grade level. We are primarily still using asphalt shingles, steel nails, fiberglass insulation, gypsum wallboard, and we use most of the same installation practices used in previous generations. Generally, the building materials market prefers evolutionary vs. revolutionary change. The market is highly competitive and its key players (contractors) are operating on tight margins and not inclined to bear the cost of change all by themselves. In order to be successful with a new product, a manufacturer has to make the benefit of switching very favorable for a contractor, while minimizing the difficulties involved while making the change.
On occasion, the industry is amenable to change. For example, in recent times nine feet has rapidly become the new standard wall height, and 2×6’s are used almost as often as 2×4’s for wall framing. Granite is the new standard countertop (though quartz is fast overtaking granite). And wood floors have become the most popular flooring for the main living areas, surpassing both carpeting and tile.
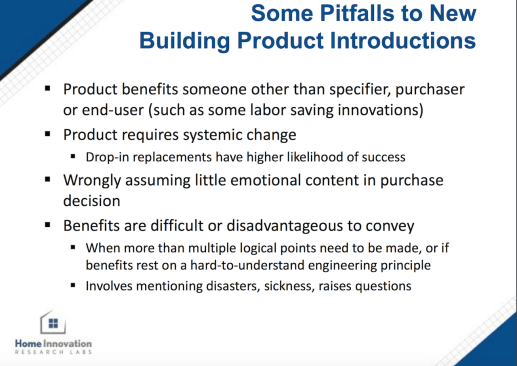
Among the many fascinating data points in Ed’s presentation of building practice trends, some of which note minuscule but meaningful new, potentially transformative trajectories surfacing in areas like basement wall materials and the use of 2″ x 6″ for interior walls, are some of the pitfalls manufacturers and/or new process providers can encounter as they try to introduce changes to this so-called “200 year-old industry, unimpeded by progress.”
Hudson’s analysis also draws from an ample knowledge-base of “failed” good ideas, revolutionary new products, game-changing processes, and can’t-miss, scientifically-validated new materials. Common mistakes, and all-too-common push-back from either a cost stand-point or a lack of interest among end-user consumers or trade partners, can lead to dismaying or confounding lack of adoption to something an innovator might believe to be a no-brainer, obvious change to make.
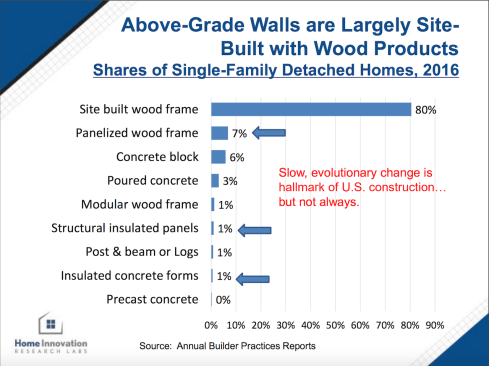
One key area of innovation in home building processes many are keen to know the near-term and ultimate outcome centers on what amount of new-home enclosures and sytems might be assembled in an offsite environment versus the pervasively practiced on-site stick-built fabrication process that has been the rule in timber-frame home construction for more than a century.
We believe that between now and 2020–two short years–a fundamental pivot will be underway that will profoundly alter the data and trends in Ed Hudson’s chart above. But the pivot will only happen if the transformation hits on all the cylinders Hudson lists below:
- Reduce skills required (unskilled worker to do job of journeyman)
- Reduce crew size (run more crews with same workforce)
- Eliminate need for a trade—one trade does work of two
- Fewer trips to the jobsite
- Reduce fatigue & jobsite injuries to keep workers longer
- Allow for easier payment of workers by piece rates
- Cautions: saving time for one worker does not always
- translate into overall time savings
- Focus on savings in time-consuming activities
Check out Ed Hudson’s terrific presentation on what changes and what doesn’t change in home building, and why that matters, here.